Condition-based Monitoring:
Use data, increase plant performance
Episode 11
Production data and their visualization
The first episode of the actuator podcast already dealt with condition-based monitoring (CBM). The focus at that time: the technology and the teaching of the system. Episode 11 of Drehmoment – der Antriebspodcast focuses on the user. It’s all about data and visualization. Podcast host Robert Weber talks with user Jakov Perisic of Molson Coors, a multinational brewing group that has many prominent beer and beverage brands in its portfolio; Ian Rowledge, production data collection and visualization specialist at LineView; and Virgil Ioan Lupu of Danfoss Drives. Lupu is part of the team that developed condition-based monitoring with frequency converters.
The three experts agree: Data must be turned into meaningful and easily understandable information in order to get more intelligence into the production processes in the next step. Jakov Perisic in particular is looking for a simple and practical solution: "With CBM, we don’t just want to make repairs more efficient, we want to be able to run the plant longer. The focus is on our in-house platform, which is filled with data and assures us of transparency in the processes." But the first step, filtering important information from the vast amount of data, is not trivial. The three experts explain how they manage it in the podcast conversation.
Two years of roller coaster - Interview with Jakov Perisic from Molson Coors
Jakov Perisic is senior manufacturing excellence lead at Molson Coors. The beverage specialists use frequency converters with CBM functionality from Danfoss Drives and collect the data and information from different systems in an in-house platform. The pandemic demanded a lot from him and his team. The digital transformation hit production hard. He explains in an interview how he and his team deal with this and how they optimize processes together.
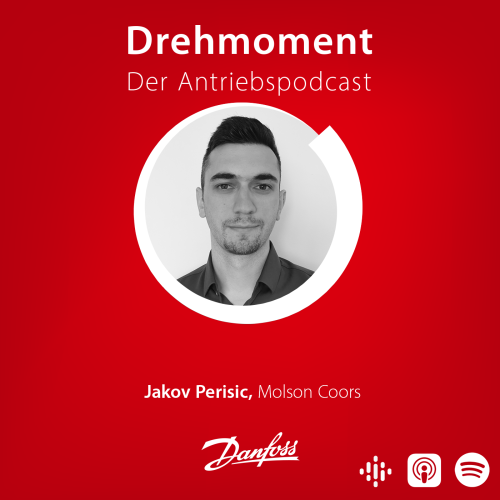
How is digitalization changing production at Molson Coors?
We sent many colleagues to the home office during the pandemic. They had to work from home. That worked out, thanks in part to our new processes. Most of our processes were already highly automated before the pandemic. But in the pandemic, we learned to appreciate the value of data even more. We understand our plants better – thanks to condition-based monitoring. My team knows error modes better now. Our approach: We don’t want to make the repairs more efficient, but we want to be able to run the plant longer. The focus is on our platform, which is filled with data and assures us of transparency in the processes.
You use the Lineview platform and also the Danfoss data runs into the system, correct? How difficult was that?
Not difficult at all. You only need one push and one pull factor. We quickly understood that we have limited resources, for example, limited maintenance times and they are getting shorter and shorter – especially in the high season. We can’t afford to stop there. Every intervention, every activity must have a good reason and we must know exactly what we are doing. I always compare it to a Formula 1 pit stop – going in and coming out. Push and pull guarantees us that we do nothing for nothing. The implementation was not difficult. One challenge was the questions: What do we actually want to monitor? What does that get us monetarily and where do we measure? Where do we get the data – in the control cabinet, on the assembly line?
What convinces you about CBM?
Quite simply, the system not only tells us that something is going to happen, but it also informs us where the problem is, for example in the transmission. The information from the data is very detailed and that is important for us.
What is the importance of the usability of the system?
We have different users and not everyone needs the same information; the team management wants to have the overview. The worker on the production line wants to keep an eye on his machine. We have different roles and the system must be able to map them. For us, that’s good UX. Because we want to go one step further with the information. We not only want to know what the condition of our equipment is, for example our frequency converters, but also how it affects our end product. Our vision: In the end, the machine or the Danfoss component suggests a solution to us.
Sounds like process optimization, predictive maintenance and machine learning?
Yes, all that. Unfortunately, however, no one can give us advice from the machine yet. But we are now working on it ourselves internally.