Achieve CO₂ neutrality:
Taking our own Medicine
Three steps to CO₂ neutrality with energy efficiency measures
Companies are increasingly focusing on the CO₂ neutrality of their buildings and production facilities. This saves costs. It also helps to reduce the ecological footprint. Danfoss is also working on becoming CO₂-neutral by 2030 at the latest.
Energy efficiency is climate protection
Global energy and climate protection targets play an important role here. In order to achieve decarbonization, politicians have initiated the energy transition. But how exactly can the industry implement this? On the one hand, non-sustainable energy sources can be replaced by regenerative energy supplies using renewable energies.
However, the most sustainable energy is the energy that is not consumed in the first place. Measures to increase energy efficiency aim to reduce energy consumption in buildings, industrial and production facilities and the transport sector. The motive behind this is simple: energy that is not needed does not have to be compensated for. This makes energy efficiency an extremely important pillar of decarbonization.
Implementing energy efficiency is easy
In addition to the classic measures to increase efficiency, such as improved building insulation, insulated windows or the use of LED lighting, one area often goes unnoticed: the drive technology in buildings, systems and infrastructure and their control.
A considerable increase in efficiency, and therefore savings in energy, emissions and costs, can easily be achieved in electrical drive technology with technologies that have been available for a long time, such as speed control using frequency converters. 60 to 70% of applications with electric motors in industry and building technology benefit from demand-driven speed control.
The success story of the Danfoss production site in Nordborg, Denmark, shows that increasing energy efficiency is an important cornerstone for CO₂ neutrality in buildings. Numerous energy efficiency projects initially reduced energy consumption as a first step. Let this inspire you for your own path to CO₂ neutrality.
With the Danfoss 3-step approach to CO₂ neutrality in your building
In 2022, the 250,000 m² plant site in Nordborg achieved climate neutrality (in Scope 1 and 2, i.e. emissions from purchased energy and from sources owned or controlled by Danfoss). Based on Danfoss’ 3-step approach, you will also receive helpful tips for your decarbonization project.
In three simple steps:
Emission reductions at the Nordborg plant site
Reduce with energy efficiency: reducing energy consumption
First, energy consumption was reduced by using energy more intelligently and cost-efficiently. In addition, Danfoss used technologies to control and monitor consumption so that energy is only used in the amount that is absolutely necessary for an optimized process. To this end, those responsible implemented a series of technical projects and improvements in order to achieve considerable savings.
This first step is used at every Danfoss location worldwide. Danfoss focuses, for example, on technologies for controlling cooling, heating and lighting in buildings. Danfoss also uses various technologies in its production facilities to control the energy consumption of the machines. The hidden champions of energy efficiency here are also ventilation systems. This is where the greatest savings can be realized. You can read the reasons for this in this article. 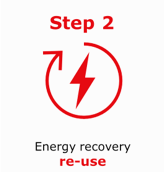
Re-use with energy reuse: Re-use of surplus heat
Excess heat is the world’s largest unused energy source. Recovered surplus heat from Danfoss production facilities, data centers, wastewater treatment plants and supermarkets flows into the internal district heating network to heat buildings at the Nordborg site. The resulting energy savings have helped to significantly reduce the temperatures in the plant’s heating network from 145 °C to 67 °C.
Re-source through the use of renewable energies: Procurement of green electricity
The remaining heat requirement is covered by reusing surplus heat, green district heating and natural gas.
The remaining emissions from natural gas will be covered by biogas certificates from a local biogas plant until they expire. Electricity requirements are mainly covered by solar panels and power purchase agreements with suppliers of climate-neutral energy. The estimated payback period for all the investments described to achieve CO₂ neutrality is 3 years.
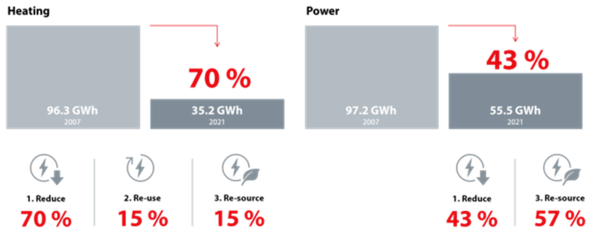
Implementation in all Danfoss buildings
Re-use in Nordborg with heat pumps for heat recovery
Heat is a by-product that occurs in almost all production processes. Instead of discharging the heat unused into the atmosphere, it can be put to better use and converted into district heating. Four industrial heat pumps are being used at the Danfoss site in Nordborg. In 2022, these heat pumps generated 5,572 MWh of heat, which corresponds to 310 Danish households. All heat pumps used are equipped with Danfoss frequency inverters to ensure maximum energy efficiency.
In addition to the main building in Nordborg, other Danfoss sites are also gradually achieving the goal of CO₂ neutrality. This also applies to the factory on the Danfoss campus in Grodzisk, Poland. All production machines and heating, cooling and ventilation systems there use green electricity. Fossil fuels have been replaced by electricity. In addition to electrification and the use of renewable energies, the focus here was also on energy efficiency. More than ten large and small energy-saving solutions were incorporated into the development of the new factory.
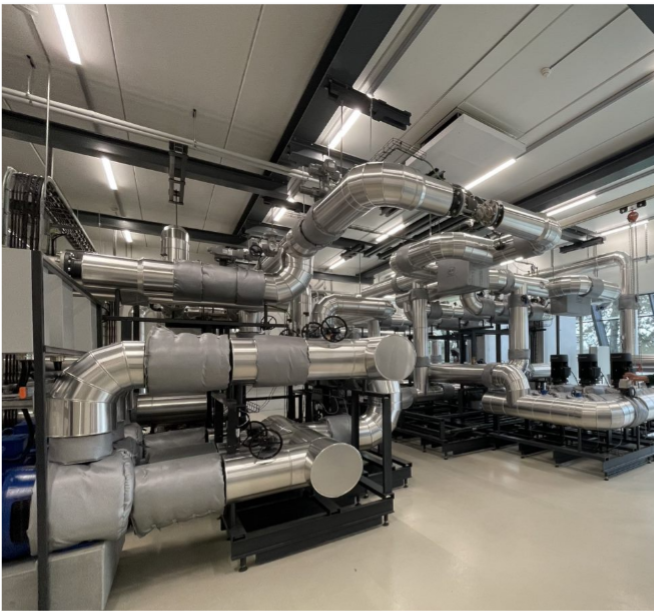
Reduce in the ventilation center of the Danfoss factory building in Grodzisk, Poland
Eight Klimor ventilation units are used to ventilate the production hall, warehouses and laboratories. They are equipped with highly efficient double cross-flow heat exchangers that enable up to 90 % of the heat to be recovered from the halls’ exhaust air. In order to create comfortable working conditions in all areas and to control the operation of the fans in the fan units, 16 Danfoss frequency inverters from the VLT® HVAC Drive FC102 series in the power range from 1.1 to 18.5 kW are used for pump, fan and compressor applications.
Energy savings and thus emission savings of up to 50% could be achieved through demand-based control with frequency converters.
Another important aspect of improving energy efficiency was the use of data collection and processing technologies. All inverters have condition-based monitoring (CBM) and are connected to DrivePro Remote Monitoring®. These measures reduce downtime in the factory and increase the efficiency of all maintenance work.
Reduce at the new Danfoss Campus in Offenbach
In addition to retrofitting existing buildings, Danfoss attaches great importance to equipping new buildings with highly efficient technologies. A current example is the Danfoss Germany sales center "Campus Kaiserlei in the Frankfurt area", which opened in August 2023.
One application that benefits from increased energy efficiency through the use of speed-regulating drive technology is the refrigerated cell (also known as a small kitchen cell) in company restaurants. The application is a so-called hidden energy efficiency champion, as the refrigeration compressor (also from Danfoss) and the two associated frequency converters are concealed in a plant room in the basement of the building. Two inverters from the VLT® Refrigeration Drives FC 103 series are used, with power ratings of 15 and 1.5 kW.
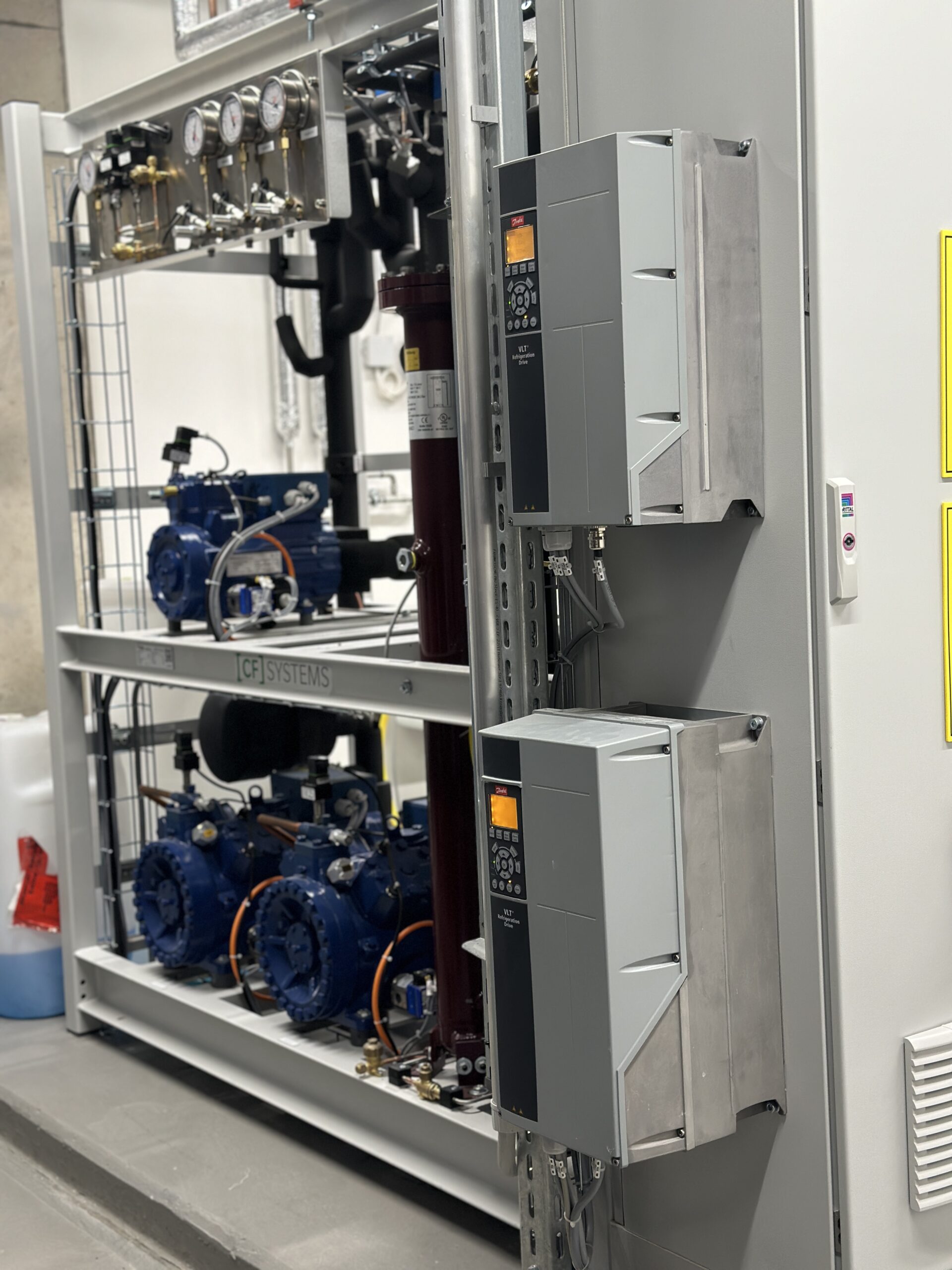
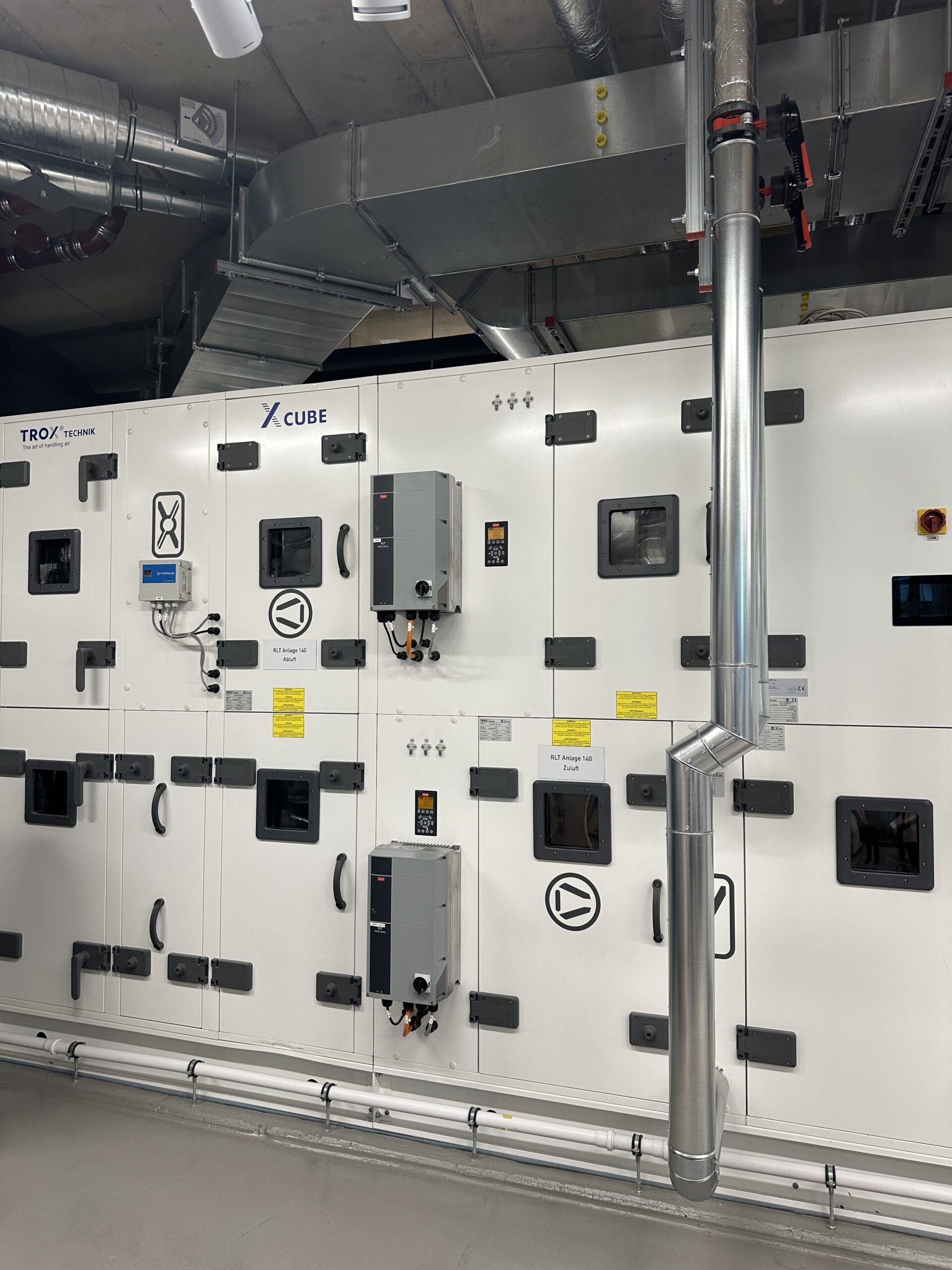
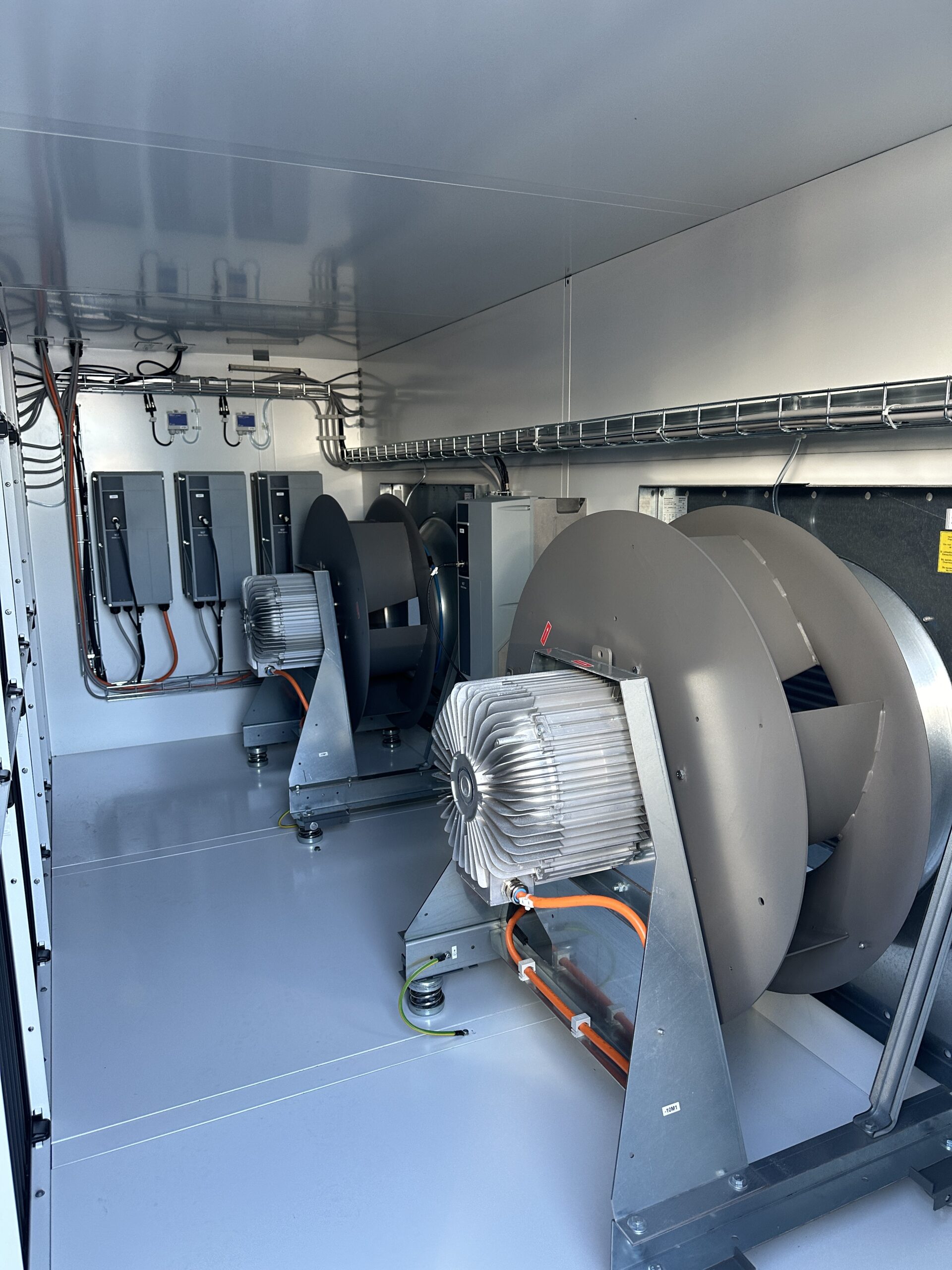
Frequency inverters installed in the Danfoss building in Offenbach
The ventilation systems are located on the roof of the new Danfoss building, in which four ventilation units, each with two VLT® HVAC Drives FC 102 series inverters, are installed. Another ventilation system with speed-regulating frequency converters is installed in the showroom, a walk-in technical room. The frequency inverters drive the fans for supply and exhaust air in the ventilation system, thus ensuring optimum room air conditions and reducing energy consumption to exactly the required level.
The following calculation shows how much energy and costs this saves.

Resource about energy storage in the Danfoss factory building in Grodzisk, Poland
Today, Danfoss buys certified green renewable energy from suppliers in Poland. The aim is to use photovoltaic modules in the future in order to cover all energy requirements from the company’s own sources.
Even when generation capacities fluctuate, for example due to changes in the weather, the energy demand must be constantly covered. To do this, the plant needs energy storage systems that store surplus energy during periods of high production and then release it when the energy from the photovoltaic system is limited.
Frequency inverters from Danfoss are a key element here, as they ensure efficient energy conversion. They are responsible for converting energy from the grid or the photovoltaic system when charging the battery, but also for converting direct voltage from the battery when feeding alternating current into the grid.
Danfoss is your decarbonization partner
Discover together with Danfoss experts Daniel and Christian how you can best tap into energy efficiency potential to get a step closer to CO₂ neutrality in your building.

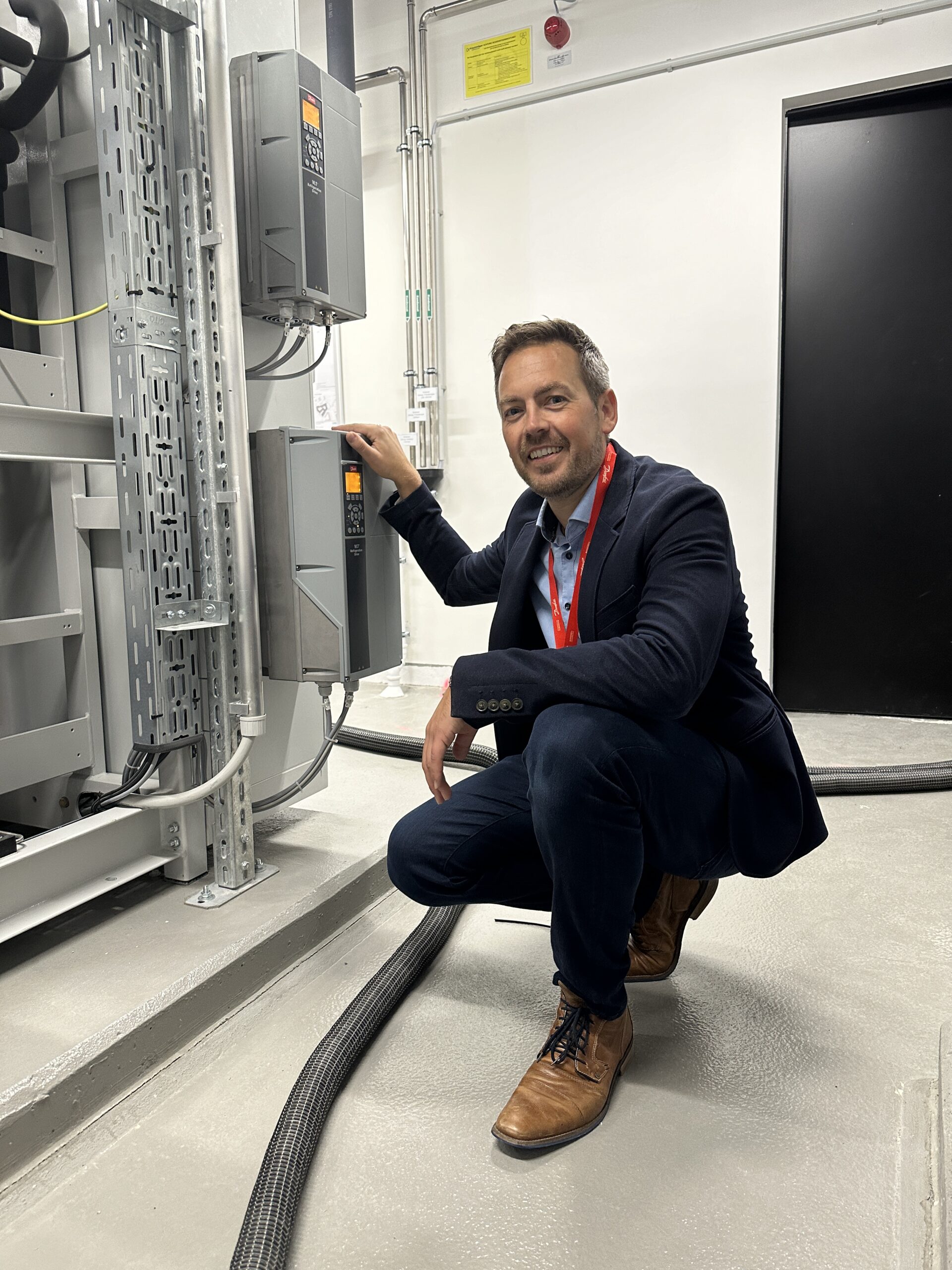